March 29, 2022
OKRs vs. Lean Methodology
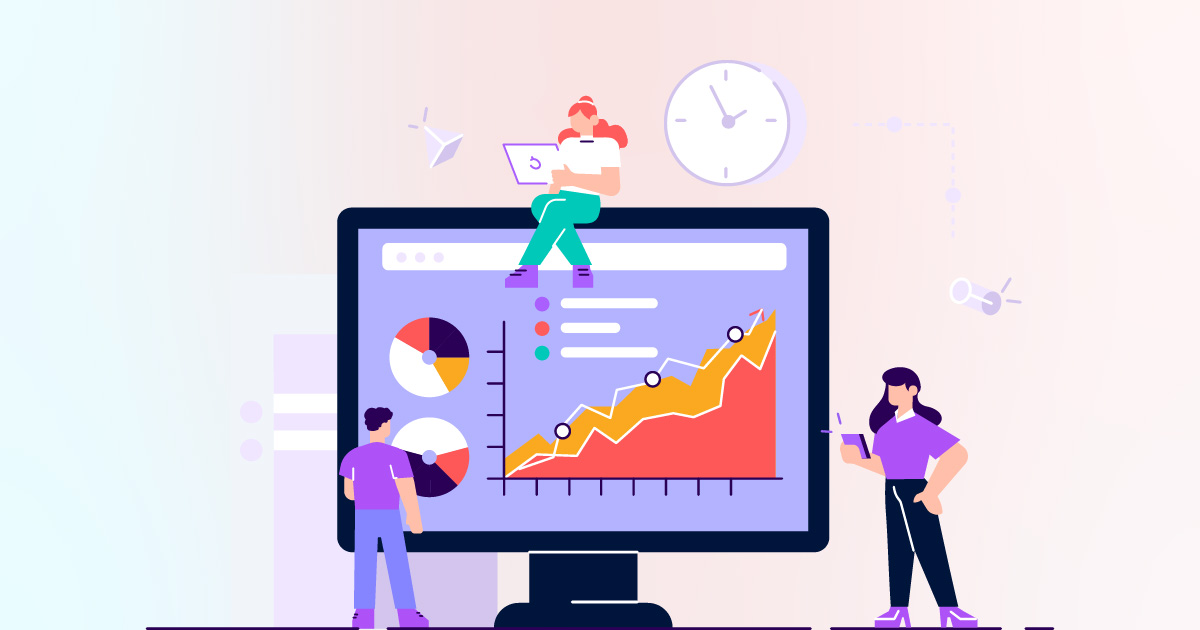
Objectives and Key Results (OKRs) are all about goal setting in a trackable matter. In contrast, A3 or lean methodology pertains to waste minimization to maintain a competitive edge. Irrespective of the waste being workflow-related or physical, OKR and lean methodologies complement one another to accomplish the high-end organizational goal. As you employ these methodologies together, you can quickly determine what matters. You thus get the task done in an efficient, time-bound manner, honing your organization’s performance.
What is Lean Methodology?
A3 management or lean methodology is a system founded on building structured opportunities for people so that they can learn in the way that is the most natural for them. This learning may come from mistakes, experience, and even plan-based trial and error. A3 management is a structured problem-solving and continuous-improvement approach that Toyota employed first, and since then, it has been used by lean-manufacturing practitioners. This lean six sigma methodology offers a stern and straightforward process that guides workers’ problem-solving efforts. This problem-solving tool encourages collaboration, learning, and personal growth. The acronym “A3” is deduced from the specific paper size used to outline ideas, goals, and plans throughout the A3 process.
Toyota uses A3 reports to solve problems, suggest policy changes, and report project status. The objective of an A3 report is to recognize and communicate the crucial project information and ease decision-making. The report should fit on one page easily. Featured as a lean tool ideal to solve relatively short-duration Kaizen improvement activities, an A3 report may not prove helpful in a DMAIC environment or the case of more complex projects.
Lean Strategy Example
Let’s say you are a manager for airplane safety maintenance. Suppose you have a labeled method with specific milestones in place. In that case, you can surely enhance productivity and mitigate the high-level costs related to wasted time, such as ensuring flights leave on time. An A3 or lean strategy is all about your commitment to recognizing targets to help assure a smoother workflow, implying less time wasted.
What are OKRs?
Objectives and Key Results or OKRs refer to a collaborative goal-setting methodology wherein individuals and teams set ambitious, challenging goals with measurable results. This practical goal setting and leadership tool enables you to communicate what objectives you wish to accomplish and what key results help meet the objectives. The OKR system creates alignment, tracks progress, and boosts engagement around measurable goals. Some of the world’s renowned organizations, including Google, LinkedIn, and Twitter, set and enact their strategies leveraging OKRs.
The OKR Formula
Typically, OKRs are written with an objective at the top, and there are 3-5 key supporting results below that objective. They are written as a statement:
I will (Objective) as measured by (Key Results).
To learn how to write OKRs the right way, look at these OKR Examples by Department.
OKRs vs. A3
Though both the methodologies value learning and improvement over time, there are a few differences.
- While A3 is more process-driven and operational than OKRs, your objectives and key results focus on your organization’s future, assuring that improvement is made towards that mission and vision.
- Another area where OKRs and Lean Strategy diverge is the fundamental focus Lean puts on instant value. To put it in simple words, A3 is meant for shorter-term projects. The OKR framework involves setting short and long-term goals to maximize accomplishment.
- Besides, A3 is highly project-driven in its approach at the team level. OKRs, on the other hand, emphasize the organization on success as well as improvement, with teams using this methodology to achieve their set targets.
How does A3/Lean Strategy Complement OKRs?
The fundamental principles of Lean may be used to increase waste elimination, besides process improvement. The five key tenets that sound pretty familiar to the followers of OKRs are:
- Define value from the end customer standpoint by product family.
- Recognize all the steps in the value stream for each product family, eradicating steps that fail to create value.
- Ensure that the value-creating steps happen in a tight sequence. The product thus flows towards the customer without any hassles.
- After introducing the flow, allow customers to pull value from the next upstream activity.
- Once the value is specified, value streams are recognized, wasted steps are eradicated, and pull and flow are introduced. The process starts again and continues until a perfect state is reached, wherein the ideal value is created without any waste.
Why You Need OKRs and Lean Strategy Together?
A3 or lean methodology and OKRs complement one another well, offering enough direction into the future. Your teams can thus focus on the problems they must solve first and processes that should be improved, and also for what reasons. After all, there should be strategic clarity and alignment on where we are all rowing as a team while allowing teams to fix on their ores, boats and, finally, brush up on rowing skills. Unlock:OKR plays a crucial role in bringing that strategic clarity and alignment.